The global demand for concrete blocks and pavers continues to grow rapidly due to urbanisation, infrastructure expansion, and the move toward sustainable construction. At the heart of this booming industry lies one crucial question: which machine is used for block making?
Whether you’re new to concrete production or considering upgrading your current setup, understanding the different types of block-making machines and their functions is essential. In this article, we break down the types of machines used for block production, their features, and how to choose the right one for your business.
What Is a Block Making Machine?
A block making machine, also known as a concrete block machine or brick making machine, is a piece of industrial equipment that moulds concrete into uniform blocks, bricks, or pavers. These machines use cement, sand, water, and aggregate to produce solid or hollow blocks that are used in construction projects around the world.
The machines vary in size, automation level, and production capacity. Some are manual, ideal for small-scale production, while others are fully automated and capable of producing thousands of blocks per hour.
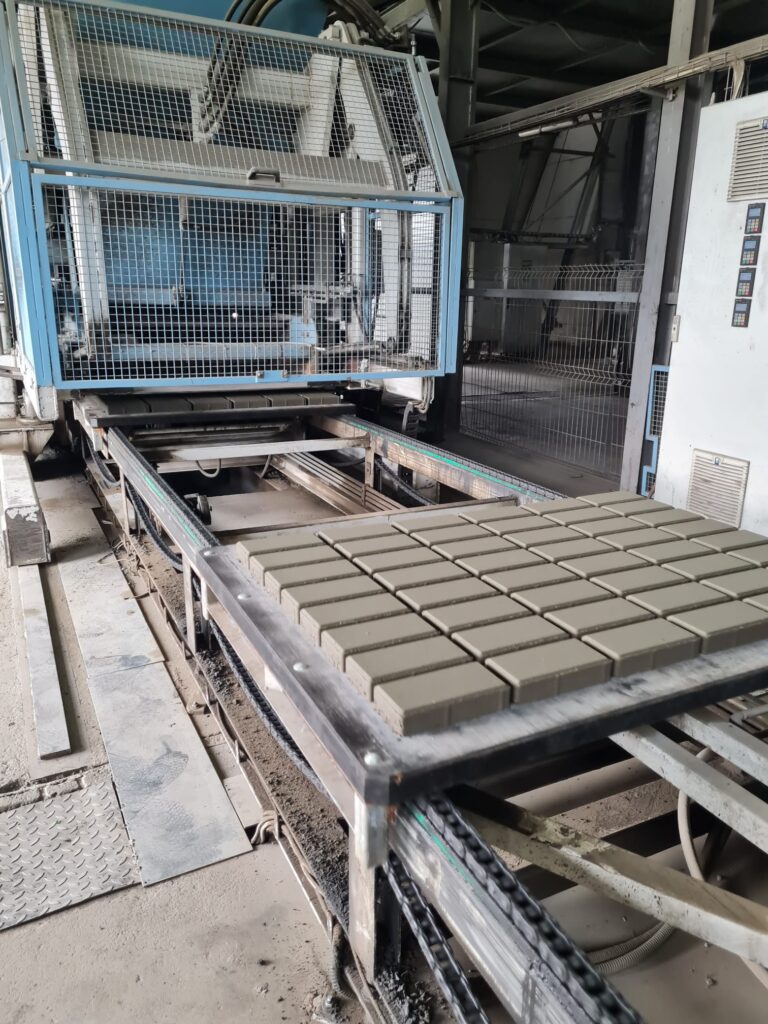
Main Types of Block Making Machines
1. Manual Block Making Machines
Manual machines are operated by hand and are typically used in smaller operations or in areas with limited access to electricity or capital investment. They require more labour and have lower production output, but are affordable and easy to maintain.
Ideal for:
-
- Small businesses
-
- Rural construction
-
- Entry-level operations
2. Semi-Automatic Block Making Machines
Semi-automatic machines combine manual control with mechanical or hydraulic assistance. They increase productivity compared to manual machines and reduce labour requirements, but still require some human involvement in block transfer or pallet handling.
Key Features:
-
- Hydraulic or mechanical pressing
-
- Partial automation for moulding or vibration
-
- Medium production capacity
Ideal for:
-
- Medium-sized businesses
-
- Growing production needs
-
- Budget-conscious upgrades
3. Fully Automatic Block Making Machines
Fully automatic machines are advanced systems that handle the entire block production process with minimal human intervention. They include automated mixing, mould filling, vibration, compaction, and ejection onto production pallets. These machines are equipped with programmable logic controllers (PLC) for high precision and efficiency.
Benefits:
-
- Consistent block quality
-
- High production output
-
- Labour cost savings
-
- Seamless integration with other equipment (mixers, stackers, curing chambers)
Ideal for:
-
- Large-scale concrete producers
-
- High-demand urban projects
-
- Exporters and contractors
Specialized Block Making Machines
While standard concrete block machines are incredibly versatile, specialized block making machines are designed to meet specific needs and production goals. These machines go beyond general hollow or solid block production to manufacture products like interlocking blocks, paving stones, and more — with precision, consistency, and efficiency.
Here’s a deeper dive into some of the most common specialized machines used in the industry:
1. Paver Block Machines
Paver block machines are tailored for producing high-density, aesthetically pleasing blocks used in driveways, walkways, and patios. They often incorporate:
-
- High-pressure vibration and compaction systems to ensure smooth surface finishes.
-
- Color mix hoppers for layered or decorative finishes.
-
- Specialized moulds that allow the production of zigzag, hexagonal, I-shape, and other interlocking paver shapes.
These machines are ideal for businesses focused on landscaping, municipal paving, or decorative concrete products.
2. Interlocking Block Machines
Interlocking block machines produce blocks with tongue-and-groove or dovetail joints that “lock” into each other during installation — reducing the need for mortar and making them ideal for fast construction.
Common applications include:
-
- Load-bearing walls in low-cost housing projects.
-
- Retaining walls and garden features
-
- Disaster-relief shelters due to quick setup and minimal resources required.
Some machines in this category are even mobile, allowing on-site block production for remote or large-scale construction projects.
3. Curbstone Machines
Designed for road infrastructure projects, curbstone machines manufacture concrete kerbs or curbs in various profiles. These machines:
-
- Use high compaction force and hydraulic pressing to achieve the durability needed for roadside conditions.
-
- May offer tilting mechanisms for easy demolding of tall or uniquely shaped curbstones.
They are commonly used by municipalities, civil engineers, and road construction companies.
4. Hydraulic Press Machines for High-Strength Products
Some projects require blocks or pavers with very high compressive strength. Specialized hydraulic press block machines:
-
- Apply up to 300 tons of pressure, far more than standard vibration systems.
-
- Create ultra-dense, wear-resistant blocks suitable for heavy-load applications like industrial yards or shipping ports.
These machines are often integrated into automated lines with curing chambers and palletizing robots for large-scale operations.
5. Multi-Layer Machines
Multi-layer machines lay down blocks layer by layer directly on the factory floor — rather than on individual pallets. This allows:
-
- Extremely high output rates.
-
- Reduced reliance on pallets (ideal for cost savings over time).
-
- Simplified curing and stacking processes.
Though they offer massive productivity, these machines are best suited for very large production facilities with the necessary space and infrastructure.
6. Egg-Laying Block Machines
Named for their mobile, self-propelled design, egg-laying machines “lay” blocks directly onto the ground as they move. These are ideal for:
-
- On-site production in developing regions.
-
- Small to medium operations with limited budget or space.
-
- Making hollow or solid blocks without the need for heavy pallet handling systems.
While they sacrifice some precision compared to stationary machines, their portability and simplicity make them a strong choice for some use cases.
By understanding and selecting the right specialized block making machine, manufacturers can maximize output, tailor production to market needs, and maintain consistent quality.
Key Components of a Block Making Machine
Regardless of type, most block making machines include:
-
- Mixing Unit – Where raw materials are combined
-
- Feeder Hopper – Delivers the concrete mix to the mould
-
- Mould & Die System – Shapes the block
-
- Vibration System – Compacts the mix for consistency
-
- Hydraulic or Mechanical Press – Applies force to solidify the block
-
- Pallet Feeder – Places production pallets for block transfer
-
- Conveyor or Stacker – Moves finished blocks to the curing area
Choosing the Right Block Making Machine for Your Needs
The right machine for your business depends on a few key factors:
-
- Production Volume: Are you producing blocks for a small project, or supplying to contractors across regions?
-
- Automation Level: Manual may suffice for entry-level production; automated systems are best for scale.
-
- Available Space: Consider your plant size and layout.
-
- Budget and ROI: Higher initial costs for automated systems may be offset by lower labour costs and higher output.
-
- Block Types: Ensure compatibility with the sizes, designs, and finishes you need.
Why the Right Production Pallets Matter
Block machines are only as efficient as the systems supporting them. One critical element is the production pallet — the surface on which blocks are moulded and transferred. Using high-quality pallets ensures consistent vibration transfer, reduces wear on the machine, and leads to longer-lasting, uniform blocks.
At Rhino Composite Pallets, we manufacture steel-reinforced composite hardwood pallets that deliver superior strength, vibration absorption, and moisture resistance — helping block producers reduce long-term costs and improve product quality.
Final Thoughts
Understanding which machine is used for block making — and how it fits into your operation — is a key step in building a successful concrete production business. From small manual machines to sophisticated automated systems, there’s a solution for every production goal.
Whether you’re expanding your current setup or entering the concrete block industry for the first time, investing in the right equipment — including your pallets — can transform your output, efficiency, and profitability.
Frequently Asked Questions (FAQs)
1. What is the most commonly used machine for making concrete blocks?
The most commonly used machine for concrete block production is the vibration and compression block making machine. Depending on the size of the operation, these machines can be manual, semi-automatic, or fully automatic. For large-scale, high-output production, fully automatic machines with hydraulic systems are preferred.
2. What raw materials are used in block making machines?
Concrete block machines typically use a mix of:
-
- Cement
-
- Sand
-
- Water
-
- Aggregate (gravel, crushed stone)
-
- Additives (optional, for color or strength enhancement)
These materials are mixed, compacted, and shaped into uniform blocks by the machine.
3. How many blocks can a machine produce per day?
Production output depends on the type and size of the machine. On average:
-
- Manual machines: 500–1,500 blocks/day
-
- Semi-automatic machines: 2,000–5,000 blocks/day
-
- Fully automatic machines: 8,000–20,000+ blocks/day
4. Do I need special pallets for block making machines?
Yes. High-performance pallets are essential for consistent block quality, efficient handling, and durability. Rhino Composite Pallets are specifically engineered for concrete block machines — combining steel, hardwood, and resin to outperform traditional wooden or plastic boards.
5. Can one machine make different types of blocks and pavers?
Yes. Many modern machines are designed to produce a variety of block shapes and sizes by simply swapping out the moulds. Some machines are even capable of producing hollow blocks, solid blocks, paving stones, and curbstones with the same core system.