Pallets play a vital role in block-making machines. They act as a foundation for the blocks during production, ensuring they maintain their shape and stay intact until they’re ready to be moved or cured.
Choosing the right pallets can make a big difference in the efficiency and quality of your block-making process.
But with so many options out there, how do you know which pallets are the best fit for your machine? Should you go for wood, steel, plastic, or something else?
Don’t worry, we’re here to simplify it for you! In this blog, we’ll walk you through everything you need to consider to pick the perfect pallets for your block-making machine. Let’s get started!
Material Considerations for Pallets
When choosing pallets for a block-making machine, understanding the materials available is crucial. Each type of pallet has its own strengths and weaknesses, which can significantly impact the efficiency and longevity of your block production process. Let’s take a closer look at the most common options:
1. Softwood Pallets
Pros: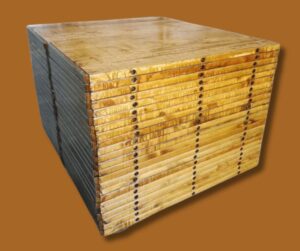
- Softwood pallets are one of the most affordable options on the market, making them a popular choice for smaller operations or businesses looking to minimize initial costs.
- They are easily available in various sizes and thicknesses, making it convenient to find options that suit different block-making machines.
Cons:
- The main drawback of softwood pallets is their susceptibility to wear and tear. With continuous use, especially in wet or humid conditions, they can splinter, crack, or warp over time.
- Softwood pallets are less durable than other materials and may require frequent replacements, which could lead to higher costs in the long run.
2. Steel Pallets
Pros: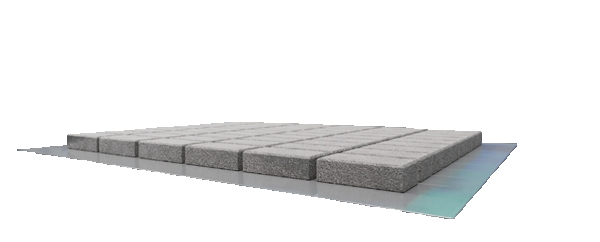
- Steel pallets are incredibly strong and durable, making them ideal for high-pressure block-making machines. They can handle heavy loads without bending or breaking.
- Their long lifespan and minimal maintenance requirements make them a cost-effective option over time.
- Steel pallets are resistant to environmental factors like moisture, heat, and chemical exposure, ensuring consistent performance in tough working conditions.
Cons:
- The biggest downside of steel pallets is their higher upfront cost compared to other materials. For smaller businesses, this initial investment might feel significant.
- Steel pallets are susceptible to rust which makes the material swell and distort. These patches can make the whole pallet distort over time which may lead to uneven concrete blocks.
- They are heavier than other materials, which can make manual handling a bit more challenging. The heavy pallets increase the wear and tear of finger car machines as well which may lead to higher maintenance costs for your equipment.
3. Plastic Pallets
Pros: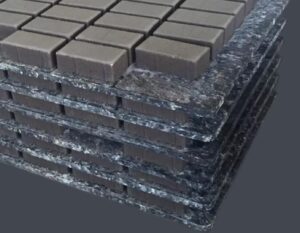
- Plastic pallets are lightweight, making them easy to handle and transport. This can reduce labor effort and enhance production speed.
- They are highly resistant to moisture, rust, and corrosion, making them a reliable choice for environments exposed to water or chemicals.
- Plastic pallets are easy to clean, ensuring hygienic conditions during block production.
Cons:
- The main disadvantage of plastic pallets is their higher cost compared to softwoodones, especially when opting for heavy-duty plastic models.
- While durable, plastic pallets may not be as strong as steel ones and could deform under extremely heavy loads or high temperatures.
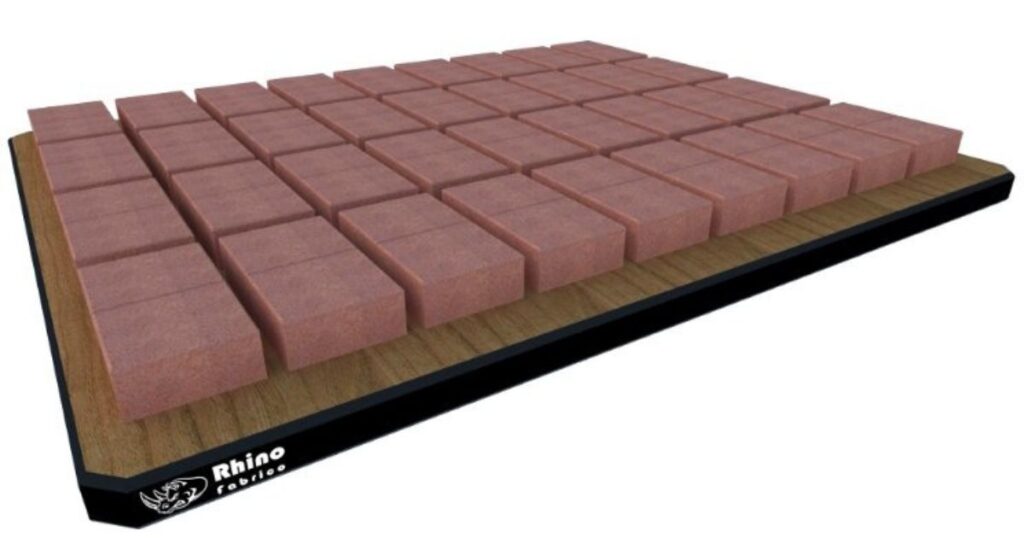
4. Composite Pallets
Pros:
- Composite pallets are a blend of materials, often combining the strength of steel with the flexibility of plastic or hardwood, offering a balanced option.
- They are highly durable and resistant to environmental conditions like moisture, temperature changes, and chemicals. This makes them a great choice for industries with demanding requirements.
Cons:
- Composite pallets are typically more expensive than softwood and even some plastic pallets, making them a better fit for businesses willing to invest in long-term durability.
- Availability might be limited compared to more common materials like hardwood or plastic, which could lead to longer delivery times.
Pointers to Consider While Choosing the Material of Composite Pallets for Block Making Machine
The right pallet material depends on your specific needs, budget, and working conditions. If you’re running a high-production operation, investing in steel or composite pallets can save money over time due to their durability.
On the other hand, for small-scale operations, wooden or plastic pallets may be sufficient to get the job done without straining your budget. Understanding these pros and cons will help you make a decision that enhances your block-making efficiency.
Size and Dimensions of Pallets
When choosing pallets for block-making machines, size and dimensions play a critical role. The right size ensures proper alignment, stability, and smooth operation, directly impacting the quality of the blocks produced. Here are the key aspects to consider:
Block-making machines rely on pallets to hold freshly made blocks as they set and cure. If the pallet size doesn’t align with the block size, it can lead to instability, causing the blocks to lose shape or even collapse during production or transportation. A correctly sized pallet ensures that blocks remain secure and well-formed, minimizing waste and maximizing efficiency.
Different Block-Making Machines and Their Pallet Requirements
Block-making machines come in various models, each with specific requirements for pallet sizes. For instance:
- Manual Block-Making Machines: These often require smaller, lightweight pallets that are easy to handle manually.
- Semi-Automatic Machines: These machines demand medium-sized pallets that provide sufficient support for larger batches.
- Fully Automatic Machines: Advanced machines require robust, precisely sized pallets to handle high-speed operations and large-scale production without interruptions. (Learn about Importance of an Automatic Brick Palletizing Machine for Concrete Block Machines)
When selecting pallets, consult your machine’s specifications to ensure compatibility. Incorrect sizes can lead to inefficiencies, machine wear, or production delays.
Key Dimensions to Consider
- Length and Width: These dimensions must match the block mold size to provide a snug fit and prevent shifting during production. Standard pallet sizes typically range from 800mm x 550mm to 1400mm x 1100mm, but custom sizes are also available based on machine requirements.
- Thickness: The thickness of a pallet determines its load-bearing capacity. For heavy blocks or high-volume production, thicker pallets (ranging from 20mm to 30mm or more) are recommended. Thinner pallets might be suitable for lightweight or smaller blocks but may lack durability in demanding conditions.
- Optional – Steel C-profile: If opting in for a steel C-profile to prolong the longevity of your pallets, don’t forget to take their thickness into account.
By choosing pallets with the right dimensions, you can ensure seamless operations and produce consistent, high-quality blocks.
Load Capacity and Strength
The load capacity and strength of pallets are crucial factors in block-making operations. Block making pallets must be strong enough to bear the weight of fresh blocks without bending, cracking, or breaking.
Load-Bearing Capacity of Pallets
Block-making pallets need to support the weight of wet blocks, which are significantly heavier than cured blocks. Hardwood composite pallets, for example, are designed to handle high-pressure loads while maintaining their shape. Assess the average weight of blocks your machine produces and choose pallets that can comfortably support this load without flexing or weakening.
For reference:
- Small Blocks: Require pallets with moderate load capacity, typically suitable for manual or semi-automatic machines.
- Large or Heavy Blocks: Need pallets with high load-bearing strength, especially for fully automatic machines producing multiple blocks in one cycle.
Choosing the Right Strength to Avoid Breakage
Pallets must be sturdy enough to withstand not only the block weight but also the pressures of production, handling, and transportation. Here are some tips:
- Material Matters: Hardwood composite pallets are a great choice because they combine the natural strength of hardwood with the durability of composite materials.
- Thickness and Reinforcement: Thicker pallets or those with reinforced cores are better suited for heavy loads.
- Quality Assurance: Always ensure that the pallets are manufactured to meet industry standards and have been tested for strength and durability.
Investing in pallets with the appropriate load capacity reduces the risk of breakage, saving you time, money, and operational disruptions.
Durability and Longevity
Durability is a key consideration when selecting pallets for block-making machines. A durable pallet minimizes replacement costs and ensures consistent performance over time.
Assessing Pallet Durability
To evaluate a pallet’s durability, consider the following:
- Material Quality: Hardwood composite pallets are known for their enhanced strength and resistance to wear and tear. The combination of hardwood and composite materials creates a product that lasts longer than traditional hardwood pallets.
- Production Conditions: If your block-making process involves exposure to moisture, heat, or chemicals, choose pallets that can withstand these conditions without degrading.
- Usage Frequency: High-frequency operations require robust pallets that can endure repeated use without compromising their integrity.
Considerations for Wear and Tear
Pallets undergo significant stress during block production, stacking, and transportation. Factors that contribute to wear and tear include:
- Moisture Exposure: Wet conditions can cause softwood pallets to warp or rot. Hardwood composite pallets, however, resist moisture and maintain their shape.
- Impact and Abrasion: Frequent handling can lead to scratches and dents. Opt for pallets with a hard-wearing surface to minimize damage.
- Environmental Factors: Extreme temperatures or prolonged exposure to sunlight can weaken some materials. Hardwood composite pallets are engineered to resist these challenges.
Choosing durable pallets ensures uninterrupted production and reduces the frequency of replacements, making them a cost-effective choice in the long run.
Maintenance and Care for Pallets
Proper maintenance can significantly extend the lifespan of your pallets, ensuring optimal performance and reducing replacement costs. Here’s how to care for your block-making pallets:
Tips for Cleaning and Maintaining Pallets
- Regular Cleaning: Remove debris, dust, and block residues after each production cycle. Use a soft brush or damp cloth for wooden composite pallets to avoid abrasive damage.
- Avoid Harsh Chemicals: Use mild cleaning agents to prevent corrosion or weakening of the composite material.
- Inspect Frequently: Regularly check pallets for signs of damage, such as cracks, rust, deflection, bowing, swelling, splinters, or uneven surfaces. Addressing minor issues early can prevent major failures.
Repairing Damaged Pallets
- Minor Damage: Small cracks or scratches can often be repaired with adhesive or filler materials.
- Severe Damage: Replace pallets with significant damage, as using compromised pallets can lead to block defects or machine malfunctions. Alternatively, at RHINO Composite Pallets, we can refurbish old RHINO pallets to near-new condition at the fraction of the cost of brand new pallets. Plus, like with brand new RHINO pallets you’ll get another 5 year warranty on refurbished pallets!
When to Replace Pallets
Knowing when to replace pallets is essential for maintaining production efficiency. Replace a pallet if:
- It shows visible signs of warping or bending.
- It can no longer support the required load capacity.
- The surface becomes uneven, affecting block stability.
By maintaining your pallets properly, you can maximize their lifespan and ensure consistent block production quality.
Cost vs. Quality
Balancing cost and quality is essential when selecting pallets for block-making machines. While it might be tempting to opt for the cheapest option, investing in high-quality pallets often proves more economical in the long run.
Initial Cost vs. Long-Term Savings
- Low-Cost Pallets: Traditional softwood pallets may have a lower upfront cost but often require frequent replacements due to their limited durability.
- Premium Options: Hardwood composite pallets, although slightly more expensive initially, offer superior durability and longevity, reducing overall costs over time.
Benefits of Investing in Quality Pallets
- Fewer Replacements: Durable pallets last longer, reducing the need for frequent purchases.
- Consistent Performance: High-quality pallets maintain their shape and strength, ensuring smooth operations and high-quality block production.
- Reduced Downtime: With sturdy pallets, you’re less likely to experience production delays caused by pallet failures.
Making the Right Choice
When considering cost and quality, think about the long-term benefits. A higher upfront investment in premium pallets like hardwood composite ones can save money by minimizing maintenance, replacement, and downtime costs.
Why Hardwood Composite Pallets Stand Out
New age hardwood composite pallets are a perfect blend of strength, affordability, and reliability. They’re built to last, ensuring you don’t have to worry about frequent replacements or interruptions in your block-making process. With their ability to perform well under pressure and resist environmental challenges, they are a smart investment for businesses looking to enhance efficiency and reduce long-term costs.
If you’re looking for pallets that deliver on quality and value, hardwood composite pallets are the ideal choice for your block-making needs.